News & Media
NEWS & MEDIA
Latest news
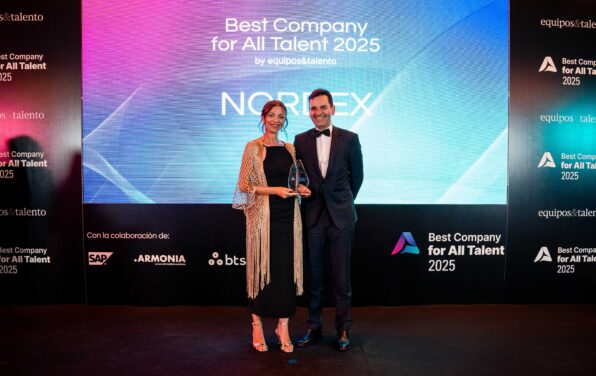
Nordex Group honoured as “Best Company for All Talent 2025” at Teatro Real in Madrid
We proudly announce that the Nordex Group has been awarded the prestigious “Best Company for All Talent 2025” prize, recognizing our commitment to fostering talent, diversity, and inclusion across all levels of our organization. The award ceremony took place on June 17 at the Teatro Real in Madrid, celebrating companies that exemplify excellence in talent […]
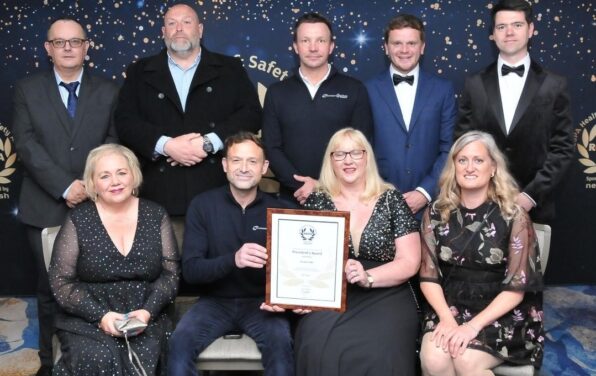
Nordex UK & Ireland honoured with RoSPA President’s Award for a Decade of Health & Safety Excellence
Nordex UK & Ireland is proud to announce that we have been awarded the prestigious RoSPA President’s Award, recognising an exceptional milestone of ten consecutive Gold Awards for outstanding performance in health and safety. Presented by the Royal Society for the Prevention of Accidents (RoSPA), this award highlights our enduring commitment to a safe working […]
Nordex Group receives orders totalling 135 MW in UK, Belgium and France
Nordex Group to deliver 21 turbines totalling 147 MW for largest wind project to date in Latvia
The Nordex Group secures new order for 160 MW in Türkiye
Media Contacts & Mailing List
FELIX LOSADA
Spokesperson
For press enquiries only:
Phone: +49-40-30030-1141
Mail: FLosada@nordex-online.com
ANTJE ECKERT
VP Corporate Communications
Mobile phone: +49 174 6833920
Mail: AEckert@nordex-online.com
INVESTOR RELATIONS MAILING LIST
Would you like to receive Nordex Group’s financial news directly by email?
SUBSCRIBE
Pictures & Footage
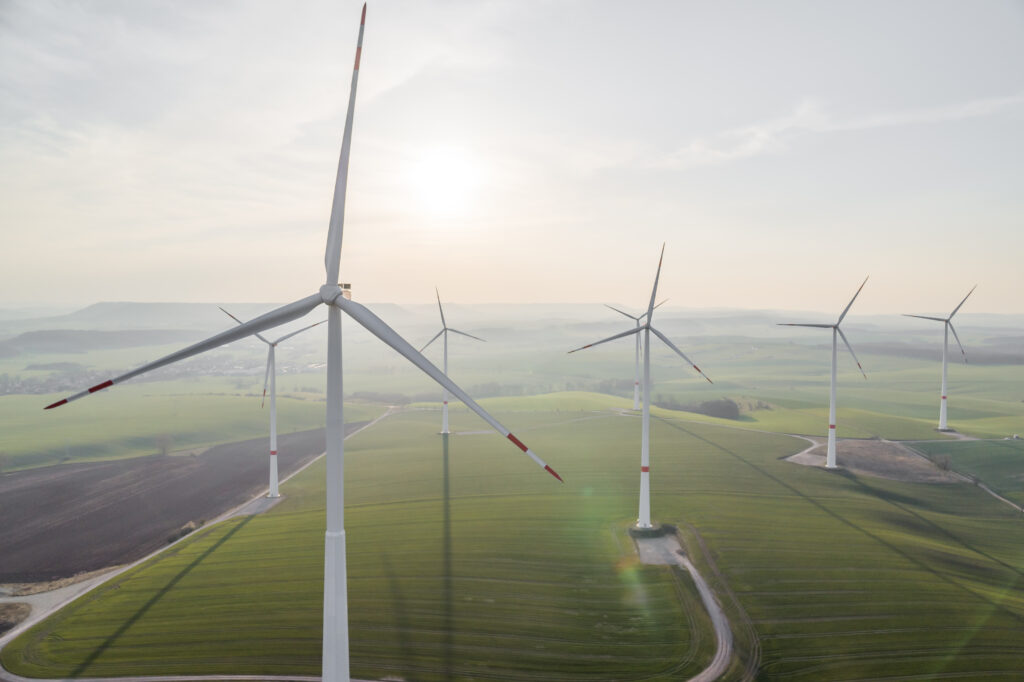
Location Germany
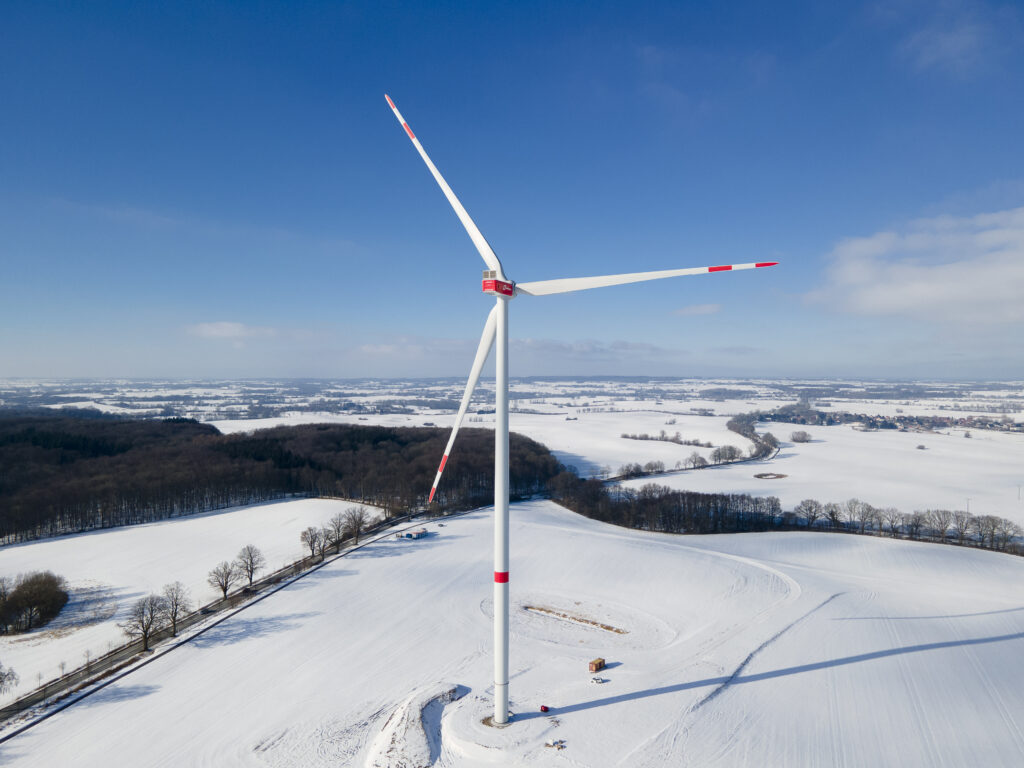
Location Germany
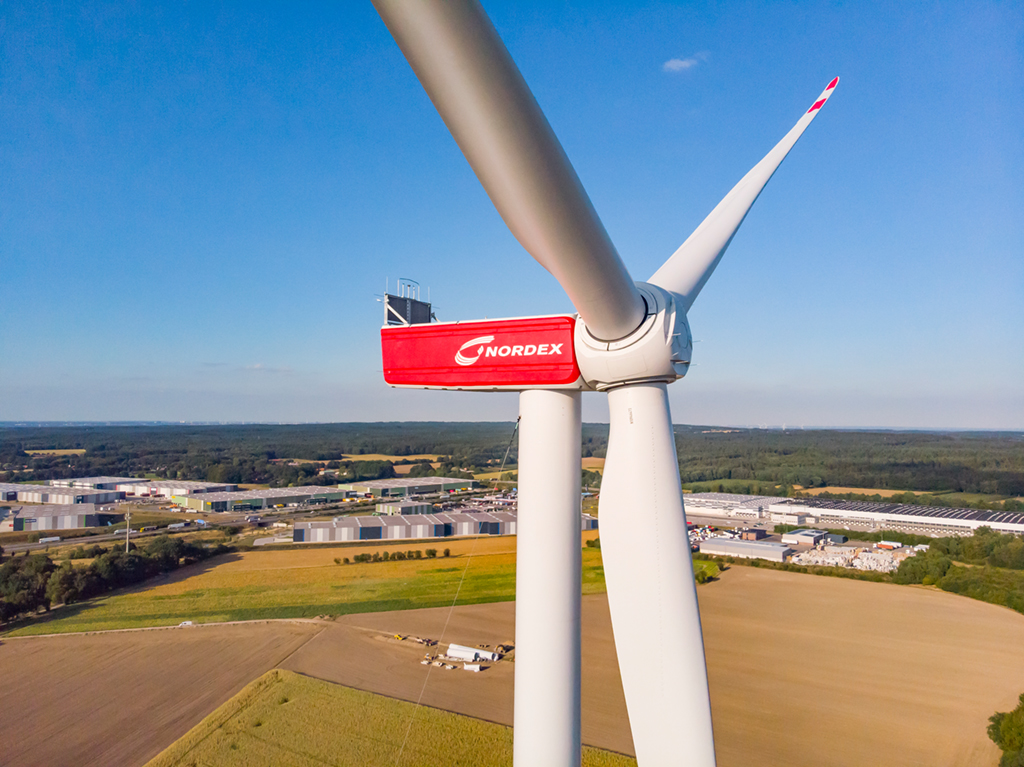
Location Germany
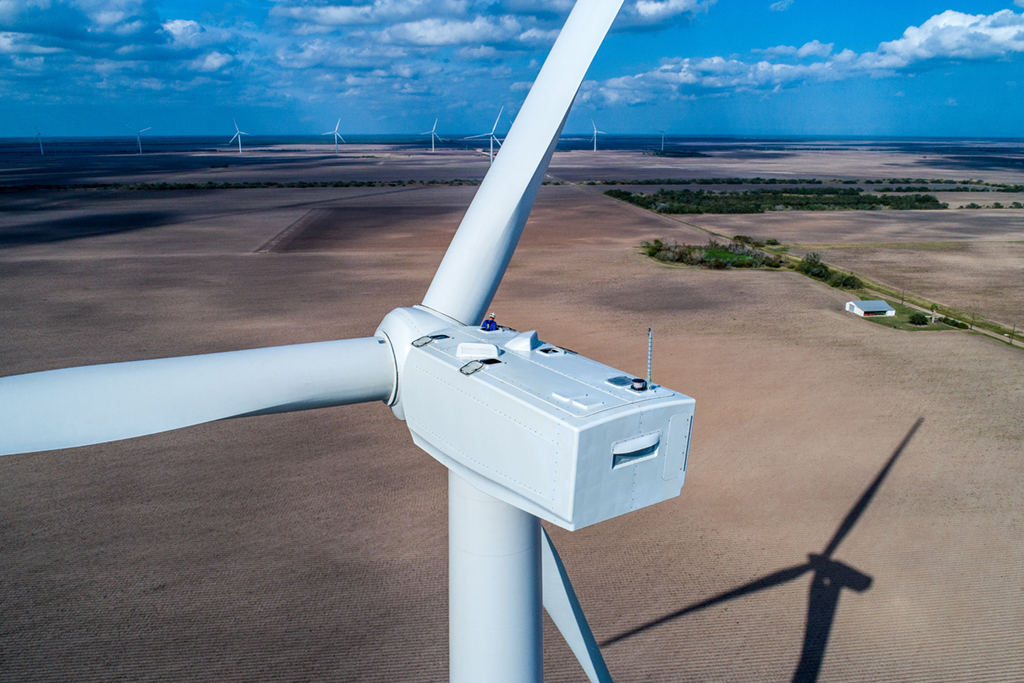
Location USA
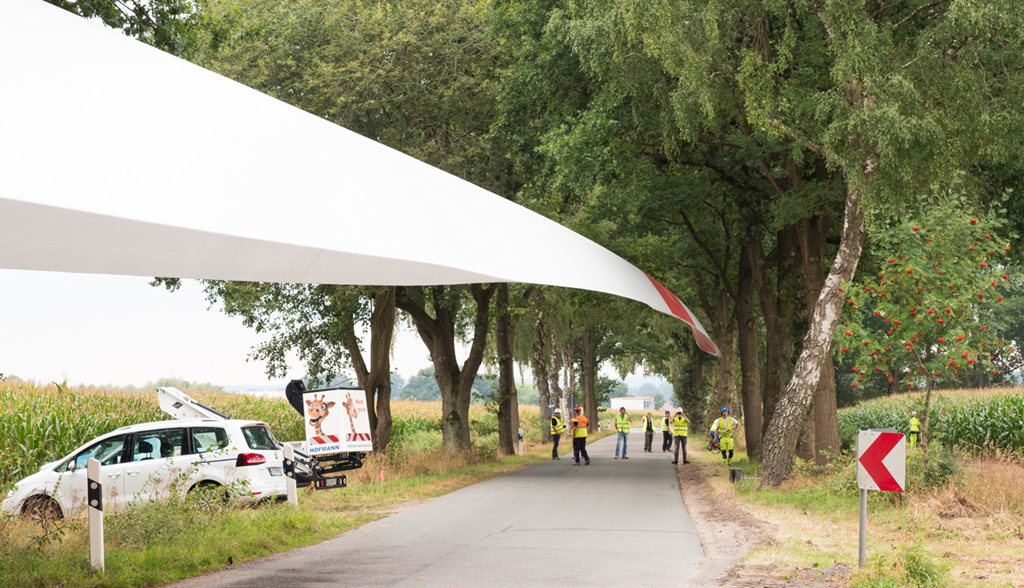
Blade Transport
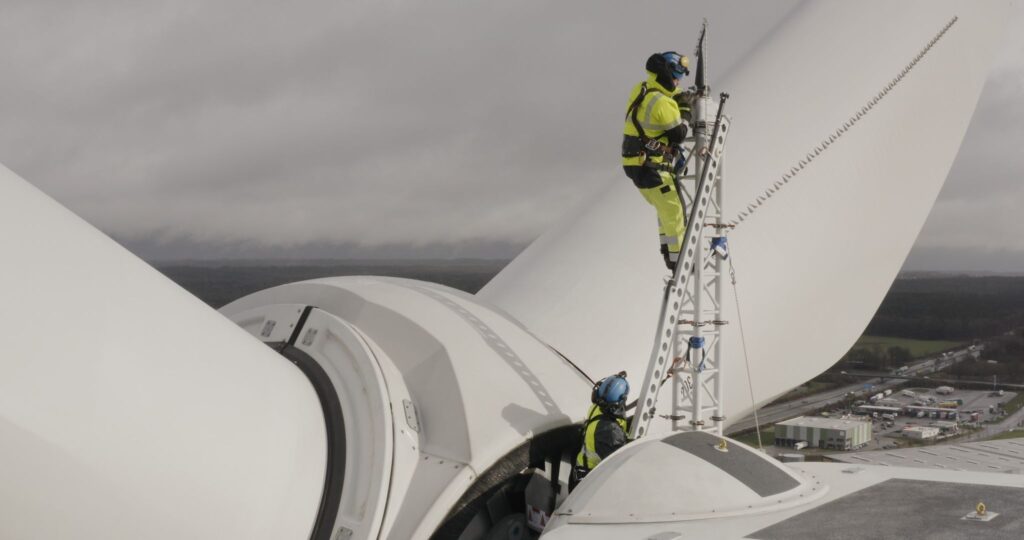
Self Hosting Crane
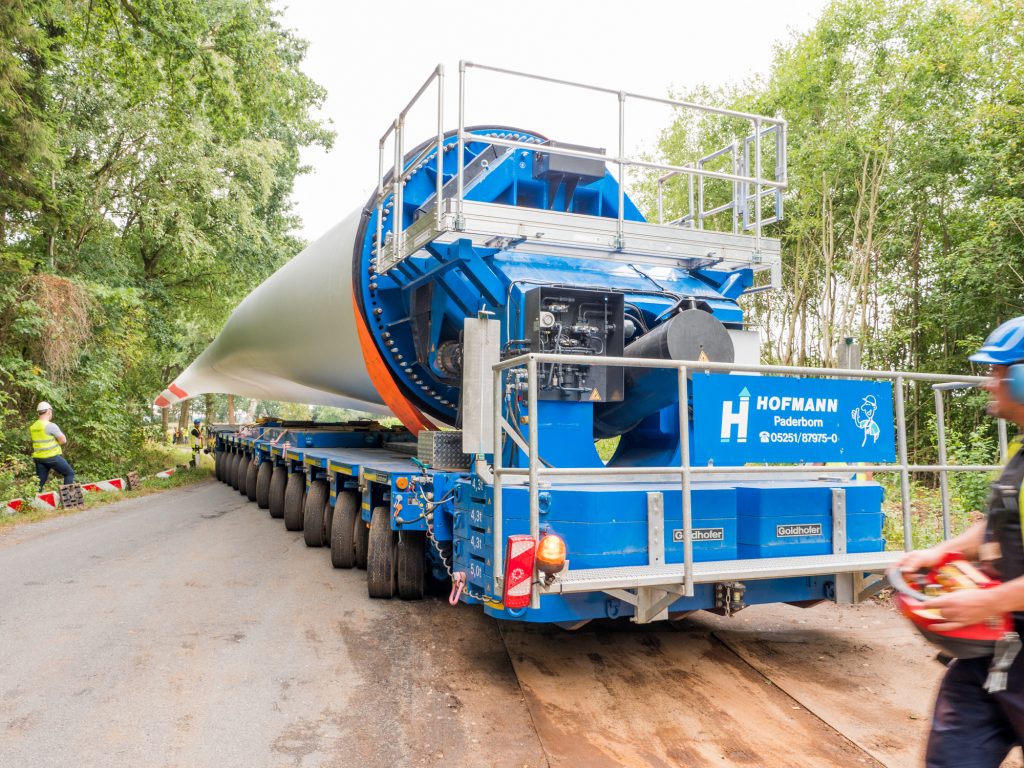
Blade Transport
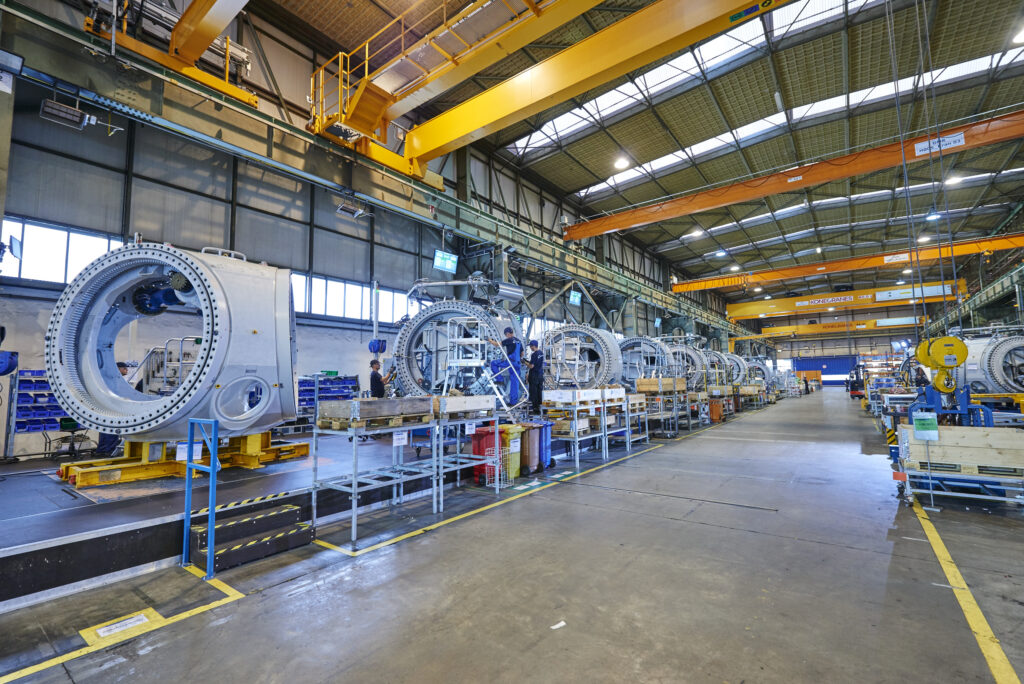
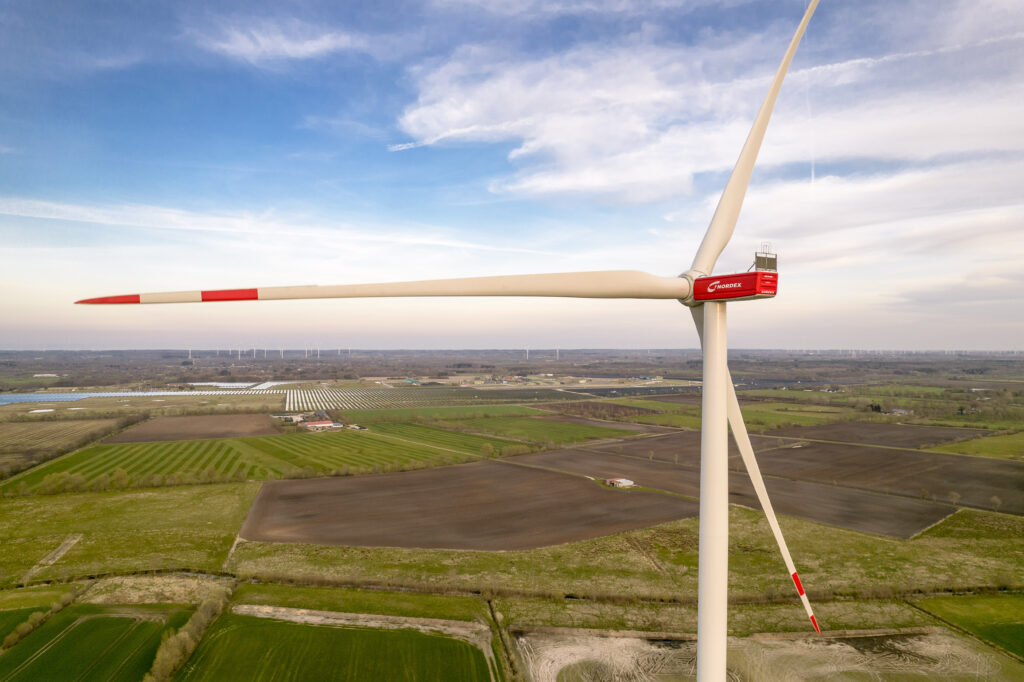
Location Germany
Social Media
Publications
Publications
Sustainability Publications
Sustainability Key Facts 2024
Sustainability Key Facts 2023
Sustainability Key Facts 2022
Sustainability Key Facts 2021
Sustainability Key Facts 2020
Sustainability Statement (Annual Integrated Report 2024)
Sustainability Report 2023
Sustainability Report 2022
Sustainability Report 2021
Sustainability Report 2020
Sustainability Report 2019
Sustainability Report 2018
Sustainability Report 2017
Sustainability Report 2016
Annual Reports
News Archive
Policies, Guidelines & Statements
QHSE Policy
Diversity & Inclusion Policy
Human Rights Policy
Whistleblower System Policy
Crime Prevention & Anti-Fraud Policy
Green Electricity Policy
Rules of Procedure for the Complaints Procedure pursuant to the German Supply Chain Due Diligence Act (GSCA)
German Supply Chain Due Diligence Act (GSCA) Policy Statement 2024
Nordex Group Forced Labor & Modern Slavery Policy 2025
Modern Slavery Statement Nordex Oceania Pty Ltd 2024
Modern Slavery Statement Nordex UK Ltd & Nordex Energy Ireland Ltd 2023
Hazardous Materials Company Standard
Life Saving Rules
Supplier Manual